Case Study:
Protective Relay Maintenance Testing
Scheduled preventive maintenance for this aluminum mill revealed a potentially damaging situation.
Objective
- Perform scheduled preventive maintenance.
Solutions
- Performed cleaning, visual inspection, and electrical testing to ensure proper performance of the protection power equipment.
- Discovered a defective electrical mechanical relay
- Arranged a time with the customer to return to the site to commission and test the new relay.
Results and Benefits
- The customer prevented a potentially catastrophic failure of their equipment.
- Equipment and operators continue to work in a safe environment.
- Customer gained more appreciation of the need for scheduled preventive maintenance.
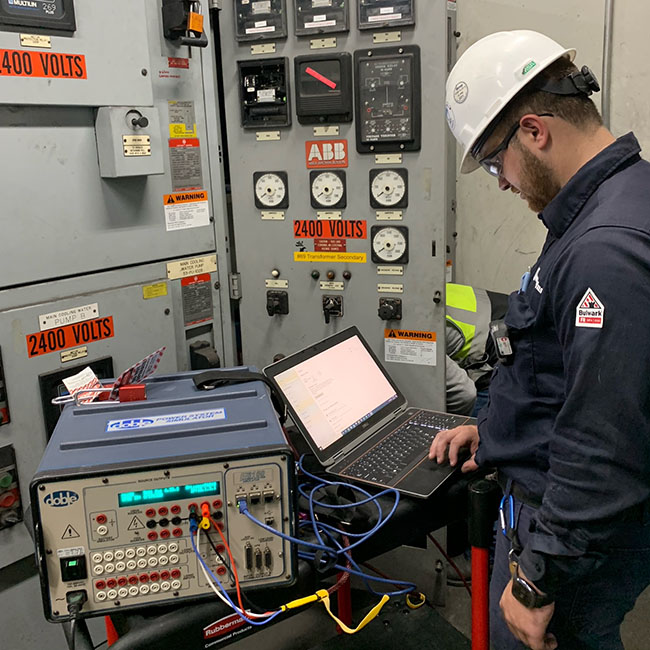
Background
The Quad Plus team was called out to this aluminum mill to perform scheduled preventive maintenance of their protection power equipment. The mill purchases mostly recycled materials from various suppliers to produce coils of aluminum alloys that are then sold to their customers who produce automobiles, cans, building materials, and more.
During the execution of the preventive maintenance service, the team discovered a defective electrical mechanical relay on the B-phase of their hot mill stand protection scheme. The relay would not trip the circuit breaker if a fault as on the B-phase. The failure to trip could lead to catastrophic equipment failure or injury to personnel.
Quad Plus Solution
The team concluded that replacing the relay was necessary to ensure proper trip functionality. We made a plan with the customer to return to the site to commission and test the new relay on the B-phase.
This event highlighted the need for scheduled preventive inspections, including protective relay maintenance testing. Without this type of proactive attention, the alternative is to simply wait for a breakdown. The result is almost always unscheduled, disruptive downtime, and serious injuries to operators can result from this type of failure. Safely completing repairs on your own schedule is always the better alternative.
Avoid Catastrophic Failure With Preventive Maintenance
The only thing worse than unexpected downtime is when an operator gets injured on the job. Both situations lead to expensive solutions for the company and could leave you exposed to legal consequences. Not to mention the painful experiences for anyone who is injured.
It is your responsibility to ensure your crew has a safe working environment and that your operations are as efficient as possible. Quad Plus makes it easy to accomplish these goals by helping you to create a preventive maintenance schedule that makes sense for your production schedule and your budget and then executing that plan with technical expertise.
Let’s get started on your preventive maintenance plan so you can be confident that your operations are safe and your production is maximized.
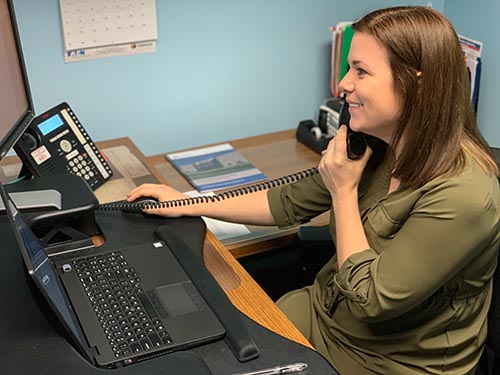