What is Preventive Maintenance for Industrial Circuit Breakers?
June 2, 2020
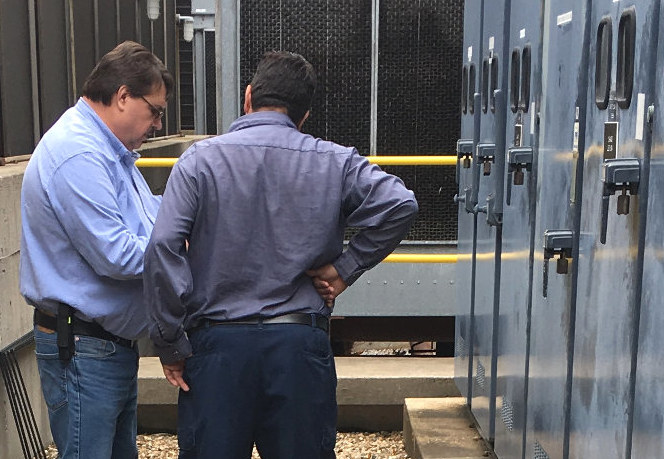
Preventive maintenance is the regular and routine maintenance of equipment that involves regularly inspecting, servicing, and repairing machinery, or systems to prevent breakdowns and ensure they continue to function efficiently. The main goal of preventive maintenance is to identify and address potential issues before they develop into more serious problems that could cause equipment failure, downtime, or safety hazards.
Circuit breakers form the foundation of safety for any industrial electrical system as they protect both your equipment and your crew from harm caused by overloaded circuits, short circuits, and other electrical problems. All protective systems should have a routine maintenance system in place to make sure everything is working as it should, and preventive maintenance will help you avoid costly breakdowns and industrial circuit breaker repairs.
Preventive Maintenance & Inspection Schedules
Regular maintenance and testing of your circuit breakers are critical as planned production interruption will always be preferred over emergency industrial circuit breaker repair. The specific schedule and routine for your breakers will depend on the type of breaker (i.e., molded case, low-voltage, medium-voltage, and high-voltage) as well as the environment in which your systems are operating. For example, a clean production environment such as electronics manufacturing may require less frequent cleaning and maintenance than one that creates a substantial amount of dust and debris.
Testing is another important aspect of routine maintenance for your industrial circuit breakers, and this routine is also determined by the type of breakers you are using. Molded case circuit breakers need very little maintenance. Low-voltage breakers should be inspected every one to three years, medium-voltage annually. High-voltage circuit breakers need the most frequent tests and inspections with a maximum of six months between checks.
When is Preventive Maintenance Required?
Preventive maintenance of circuit breakers is typically scheduled and performed based on several factors to ensure equipment reliability, safety, and efficiency. The timing and frequency can vary depending on the type of equipment, its criticality to operations, environmental conditions, manufacturer recommendations, and historical performance data.
One of the greatest dangers of deteriorating industrial circuit breakers is that they remain idle most of the time and are not in operation. Unlike the rest of your equipment where a breakdown will be noticeable, you may not notice a problem with your breakers until one fails completely and you’re looking at halting production to perform industrial circuit breaker repairs. If dirt and debris have accumulated inside the breakers, they may not be able to operate correctly. Lubrication can break down over time and become sticky and gummy. This may also prevent the parts from moving freely and functioning as they should.
That’s why preventive maintenance is important to identify any potential issues before they turn into serious and costly problems.
Routine Testing Procedures
Routine testing is generally a simple procedure that can be done onsite and without halting operations in most cases. NETA-certified acceptance testing ensures your devices are working according to the most recent NETA specifications. Key components should be inspected, including arc chutes, contacts, and connections. Contact resistance testing should be done to verify proper resistance values, and more. For low voltage breakers, primary and secondary injection testing is also completed to verify fault trip and overload protection. The exact type and frequency of testing depend on your operations, but these are some standard testing procedures that may be performed to avoid disruptive industrial circuit breaker repairs:
- Circuit Breaker Analyzer. This device tests the timing of the open and close operations of the breaker as well as the synchronism of the poles in different operations.
- Micro-ohmmeter. Resistance testing, such as those performed with a micro-ohmmeter, is necessary to avoid hot spots within the breaker and detect the possibility of imminent problems.
- Infrared Inspections. Infrared inspections are useful for finding hot spots that can be caused by defective connections and components. When an increase in resistance causes excessive heat, components may fail. Early heat detection can prevent failures.
Routine Maintenance Procedures
Some breaker types, such as molded case circuit breakers, need very little maintenance. Other breaker types should be part of a regular maintenance schedule that is frequent enough for your equipment and environment. Some common maintenance procedures may include:
- Cleaning. Dirt and debris inside the breaker can cause several problems, from failure to trip to fluctuations in the power supply. Cleaning involves removing the cover from the breaker, performing a visual inspection, and cleaning using vacuum tools or swabs and isopropyl alcohol.
- Lubrication. Lack of lubrication or the deterioration of the lubricant is one of the leading causes of breaker failure leading to industrial circuit breaker repair. Primary and auxiliary connections, pivot points, main contacts, and operating mechanisms should all be checked for proper lubrication.
- Tightening & Retorquing. The NEC has added proper tightening torque to the list of requirements for electrical connections in 2017, and this includes circuit breakers. The manufacturer of the breaker will have a recommended value printed on the breaker or listed in their literature and these values should be verified periodically.
Benefits of Preventive Maintenance
Routine maintenance and testing are far easier to work into your production schedule than unexpected downtime.
Additional benefits of preventive maintenance include:
- Enhanced Safety: Regular maintenance ensures that automation equipment operates safely and reliably. Malfunctioning automation systems can pose safety risks to workers and the production environment. Preventive maintenance helps mitigate these risks by keeping equipment in optimal condition.
- Extended Equipment Lifespan: By addressing wear and tear through preventive maintenance, the lifespan of equipment and systems can be extended. This maximizes the return on investment (ROI) for expensive automation assets.
- Optimized Performance: Well-maintained systems operate more efficiently and effectively. Preventive maintenance activities such as cleaning, calibration, and software updates help optimize performance, resulting in better productivity and quality of output.
- Cost Savings: Although preventive maintenance requires upfront investment in time and resources, it ultimately reduces overall maintenance costs in the long run. It helps avoid costly emergency repairs, production losses due to downtime, and premature replacement of equipment.
What is an Example of Preventive Maintenance?
An example of preventive maintenance for industrial circuit breakers includes a combination of visual inspections, functional testing, and cleaning. Here’s a breakdown of the steps involved:
-
Visual Inspection:
- Check for physical damage and signs of overheating signs.
-
Functional Testing:
- Test operation under load conditions.
- Verify trip settings and conduct insulation resistance tests.
-
Cleaning and Lubrication:
- Remove dust and debris from components.
- Clean and lubricate moving parts as needed.
-
Tightening and Torque Checks:
- Ensure terminal connections are tight and torqued correctly.
-
Record Keeping:
- Maintain detailed records of maintenance activities.
- Schedule next maintenance based on findings.
By regularly performing these tasks, you can ensure the reliability and safety of your industrial circuit breakers.
Preventive maintenance plays a crucial role by increasing reliability, reducing downtime, improving safety, and optimizing performance. By implementing a preventive maintenance program, you can save costs associated with emergency repairs and unplanned downtime, as well as improve the reliability and longevity of your equipment and system assets.
If you’re not sure how frequently to test and inspect your electrical equipment or what type of routine maintenance is necessary, Quad Plus can help. We’ll work with your team to develop a schedule and routine that help avoid unexpected industrial circuit breaker repair and reduce the incidence of costly downtime.
Get in touch and speak to our team for more information and support.